Chimney rebuild
Neighbours reported water ingress into the loft space and water staining on the ceilings and around the chimney breast areas of the upstairs bedrooms. Due to the age of the property we concluded that the lack of a lead tray built into the chimney stack, as well as the poor condition of the brickwork and surrounding flashings were the likely causes. We were employed to dismantle and rebuild the stack, including a new lead tray, flashings and appropriate roof repairs. We were able to source imperial sized bricks to match the existing house bricks, and salvage and reuse the existing chimney pots. The lead tray, rear back gutter and front apron are all formed and welded in house by our team.
Valley rebuild
Customer had water ingress in the loft space and staining on ceilings in the rooms below. Investigations in the loft suggested the valley area to be in disrepair and in need of works. After the scaffold was erected we were able to further conclude that as well as the valley being in bad condition, the bonding detail between the two roofs on the party wall line was very poor. We were then employed to replace the existing valley and construct a better detail between the two roofs. We started by stripping everything back until we found sound timbers, then refelting the area with a breather membrane and installing new treated tile battens. Finishing the valley off with a dry valley system that doesnt require any mortar so reducing future failure points and allowing for easy repair of damaged tiles. We then adjusted the overlapping tiles along the firewall and bedded on new ridge tiles, matching most of the other properties in the street.
Decorative chimney restoration
Working together as part of a team of other tradesmen I was asked to solve the problem of replicating the capping stones used on a number of decorative chimneys. The first step was to salvage as many parts of the cap and assemble them back together with the aid of helix bars and resin. After rebuilding the missing sections, I applied an exterior masonry filler to the surface of the entire capping stone, and sanded back to provide a smooth surface. Next I put together a timber frame that would allow me to cast the template in, and then be reused to allow future casting from the mould. The template itself was formed from a two part liquid latex system that once cured would be strong enough to support the pressure of the material used to create the new caps, but also resilient enough to survive being used multiple times without breaking. New caps were created using a proprietary concrete mix, with helix bar reinforcement around the rim.
Brick slips
A regular customer had a bit of a dilemma about what to do with a small porch that was added to their property many many years ago. The porch itself was built from LBC bricks which were starting to deteriorate. The bricks didnt match the character of the building and generally the area was an eyesore and not fit for purpose. There were a few different routes that we could go down. A complete rebuild, which would have been costly and there was some debate as to if the porch was actually supporting the house wall. Repairing where required and painting to match other sections of the property was also considered. In the end we agreed on a plan to clad the entire porch in brick slips. This removed the need to take the porch down, and would rectify the problem with the bad brick match. The window sizes were adjusted, the building was clad in a much more suitable brick match, and then repointed in a lime mortar. New bespoke windows and door were fitted, and the internals were boarded and plastered. It now serves as beautiful entrance to this period property.
Floor replacement
We were called to a rental property to investigate a suspicious movement in the floor in the kitchen. There had previously been a leak in the kitchen plumbing which had been fixed, but after several weeks the flooring was reported to be bouncy by the tenants. After stripping the flooring back the water damage was obvious. The floorboards were repaired and replaced where needed, then new underlay and flooring installed.
Face lift
A client asked us to carry out repairs to a new building they had purchased. In its original state the building had numerous defects in the render. From cracks and gouges to sections that were missing and blown. The timber windows were in a sorry state. The roof was littered with broken slates, large areas that looked to have been badly repaired, mismatching hips and ridges, asbestos soffits hanging loose and leaking gutters. By the time we were finished with the building it was looking sharp and fresh. The entire roof covering was replaced with natural slates. New upvc soffits, fascias and gutter installed to the perimeter. Windows repaired where possible, and new installed where not. The render was patched in the worse locations, and the cracks and holes filled. Then the entire building was painted to bring the property a new lease of life.
Flat roof
Customer had a leaking flat roof that was in need of replacing. The existing mineral felt system had come to end of its life span, and the underlying decking was deteriorating. We were employed initially to replace the flat roof, which included removing the original coverings, installing new OSB decking, new leadwork and a new two layer torch on mineral felt system. During the process we were asked if we could also insulate the room as there was no insulation originally installed. As the ceiling was damaged from the water ingress it was decided the best way forward would be to remove the ceiling and work from below. This had the added advantage of allowing the installation of a vapour barrier to the underside of the joists. This layer is very important as it prevents water vapour passing through the plasterboard and condensing in the roof void which can cause mould. The ceiling was then plasterboarded, skimmed and painted.
Loft boarding
We received an emergency call from a regular customer that had overloaded the ceiling joists in the loft and they were starting to collapse. We were called in to see what we could do with the challenging space. We were able to bear new floor joists off the roof plate with timber noggins and joist hangers to hold everything rigid. We then installed tongue and groove softwood floorboards to make the floor absolutely solid.
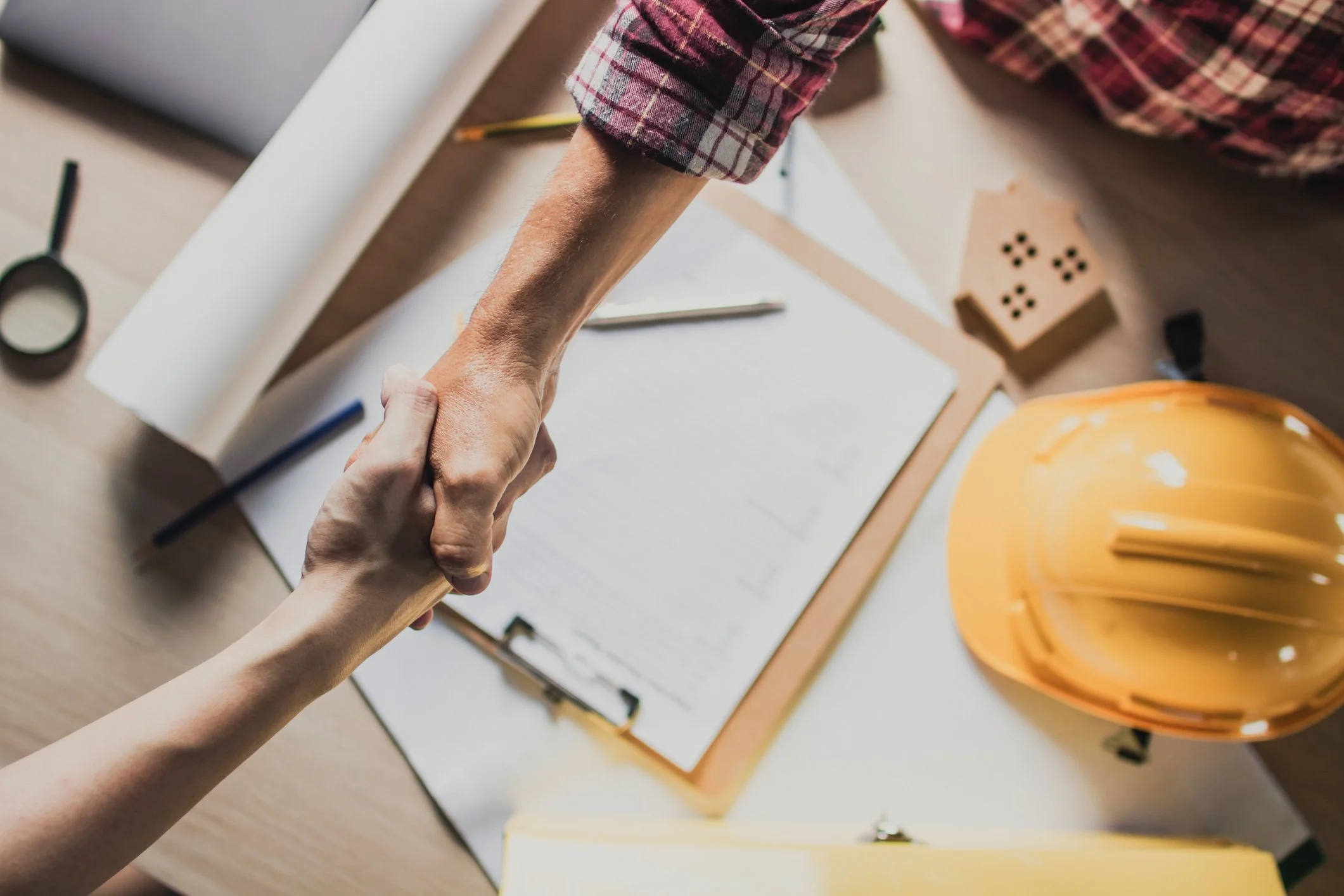
REQUEST A FREE QUOTE
Contact us for a free, non-committal estimate and site visit.